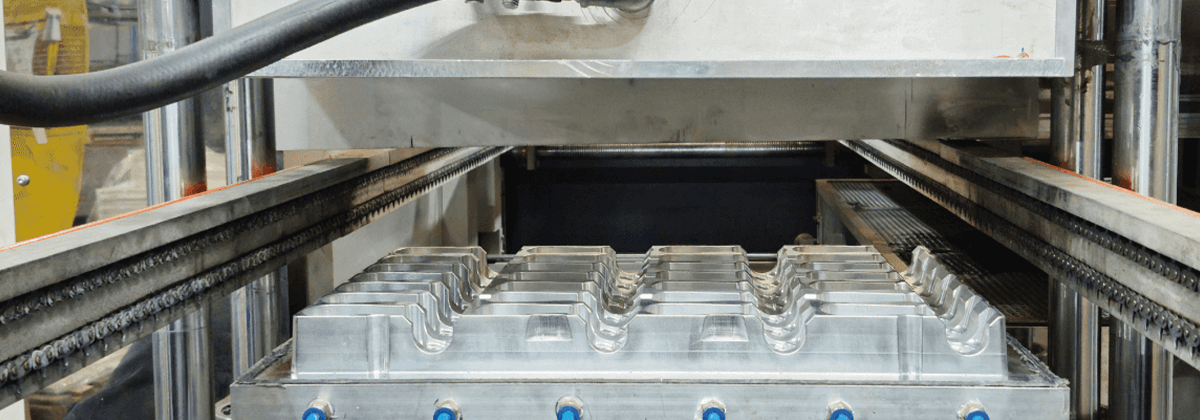
A termoformagem e a injeção de plástico são dois dos processos mais comuns de fabricação de peças plásticas, mas eles diferem em diversos aspectos, como método de produção, custo, complexidade e aplicação. A seguir, detalhamos as diferenças entre os dois processos, além dos prós e contras de cada um.
Termoformagem (Vacuum Forming e Pressure Forming).
Como funciona:
A termoformagem consiste em aquecer uma folha de plástico até que ela se torne maleável e, em seguida, moldá-la sobre um molde por meio de vácuo (vacuum forming) ou pressão (pressão positiva). Uma vez moldada, a peça é resfriada e a folha é recortada para remover o excesso de material.
Prós da Termoformagem:
- Baixo custo inicial: O molde utilizado na termoformagem, geralmente feito de alumínio ou resina, é relativamente barato em comparação aos moldes de injeção, especialmente para protótipos e pequenas produções.
- Rapidez de produção: Para peças grandes e simples, o processo de termoformagem pode ser mais rápido, especialmente em pequenas e médias tiragens.
- Versatilidade em tamanhos de peças: Ideal para peças de grande dimensão ou com formas mais simples, como bandejas, embalagens e carenagens.
- Menor desperdício de material: Pode ser mais eficiente na utilização de folhas plásticas e produzir menos resíduos, especialmente em grandes peças.
- Possibilidade de utilizar plásticos mais finos: A termoformagem é excelente para criar peças leves e de paredes finas
Contras da Termoformagem:
- Menor precisão e complexidade: Comparada à injeção, a termoformagem tem mais limitações em relação a detalhes finos e precisão dimensional. Peças altamente detalhadas ou com tolerâncias apertadas são difíceis de produzir.
- Restrições de material: A termoformagem se limita a plásticos que podem ser moldados a partir de chapas, o que exclui alguns tipos de materiais mais avançados ou com aditivos específicos usados na injeção.
- Requer pós-processamento: Após a moldagem, é necessário realizar o corte e o acabamento, o que adiciona etapas ao processo.
Injeção de Plástico
Como funciona:
O processo de injeção de plástico envolve derreter grânulos de plástico em uma máquina e injetá-los em um molde fechado sob alta pressão. Após a injeção, o plástico esfria e endurece, sendo então removido do molde como uma peça sólida. O molde é feito de aço ou alumínio e pode ser projetado para peças com detalhes finos e alta precisão.
Prós da Injeção de Plástico
- Alta precisão e complexidade: A injeção permite a criação de peças com detalhes extremamente precisos, complexos e tolerâncias apertadas. É ideal para peças que exigem encaixes ou formas muito específicas.
- Escalabilidade: Para grandes volumes de produção, a injeção de plástico é muito eficiente, com tempos de ciclo rápidos e produção em massa sem grandes variações de custo por peça.
- Grande variedade de materiais: A injeção suporta uma ampla gama de polímeros, incluindo plásticos com propriedades avançadas (resistência química, UV, alta temperatura), materiais reforçados com fibra de vidro ou cargas de outros aditivos.
- Acabamento superior: As peças injetadas podem sair do molde com um acabamento quase perfeito, muitas vezes eliminando a necessidade de pós-processamento.
- Resistência estrutural: As peças injetadas tendem a ser mais robustas e duráveis, adequadas para aplicações mecânicas ou estruturais.
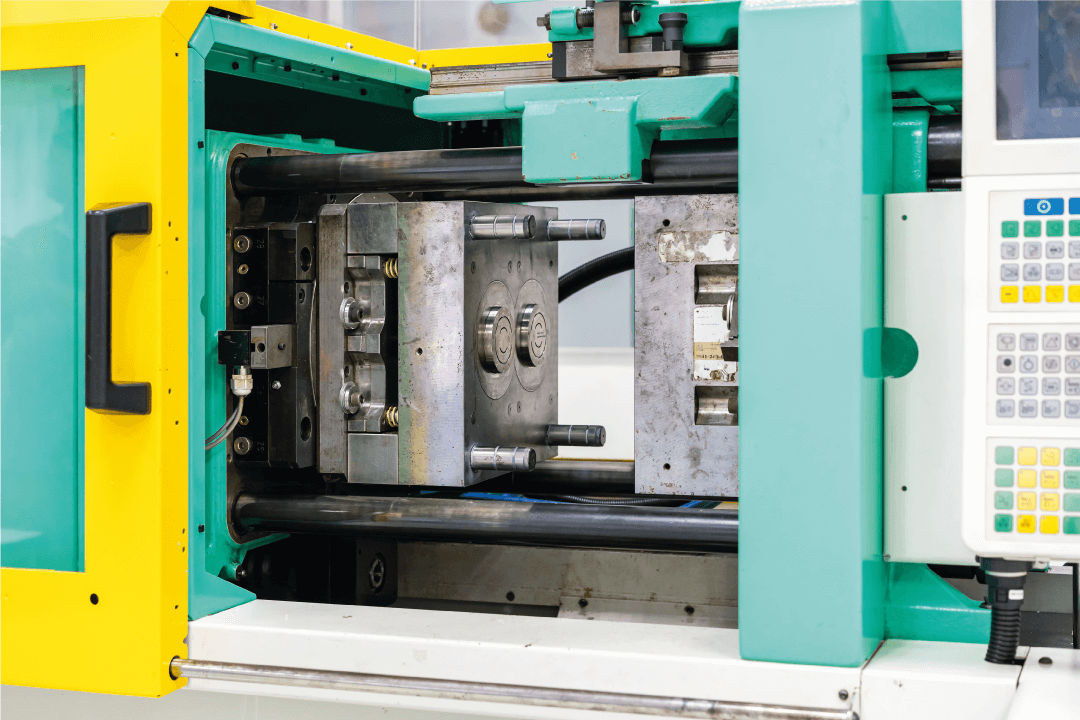
Contras da Injeção de Plástico:
- Investimento no molde de injeção é significativo, já que esses moldes são feitos de aço ou alumínio e demandam um processo de usinagem muito preciso. Isso pode ser proibitivo para pequenas produções ou protótipos.
- Tempo de desenvolvimento: O tempo necessário para projetar e construir o molde pode ser longo, especialmente em projetos complexos.
- Desperdício de material: Embora o processo de injeção seja bastante eficiente, pode haver desperdício de material nas “galerias” ou canais que transportam o plástico até o molde. No entanto, esses materiais frequentemente podem ser reciclados.
- Limitações de tamanho: Para peças muito grandes, o processo de injeção pode ser inviável devido ao custo e à dificuldade de criar moldes de grande porte.
Comparação Geral: Termoformagem vs. Injeção
Aspecto | Termoformagem | Injeção de Plástico |
Custo inicial | Baixo (molde barato) | Alto (molde caro e complexo) |
Tempo de desenvolvimento | Rápido | Lento, devido à construção do molde |
Complexidade das peças | Baixa a moderada (detalhes simples) | Alta (detalhes finos e complexos) |
Volume de produção | Pequenas e médias tiragens | Grandes volumes (quanto maior o volume, menor o custo por peça) |
Precisão e tolerância | Baixa (menos adequada para peças com alta precisão) | Alta (excelente para peças com requisitos de precisão) |
Variedade de materiais | Limitada (plásticos disponíveis em chapas) | Muito ampla (plásticos com várias propriedades mecânicas e térmicas) |
Acabamento | Precisa de acabamento adicional (recorte e pós-processamento) | Acabamento superior, muitas vezes sem necessidade de pós-processo |
Tamanho da peça | Ideal para peças maiores e mais simples | Melhor para peças menores e mais detalhadas |
Desperdício de material | Potencialmente menor, mas envolve corte e recortes de folha | Algumas perdas nos canais de injeção, mas reutilizáveis |
Quando escolher cada processo?
Termoformagem é ideal para:
- Protótipos e produções de lote piloto.
- Peças grandes, mas com design simples.
- Aplicações onde os custos iniciais precisam ser baixos e o tempo de desenvolvimento é curto.
- Indústrias como embalagens, displays, bandejas, e itens de grandes dimensões, como painéis e revestimentos.
Injeção de Plástico é ideal para:
- Produções em grande escala, onde o custo do molde pode ser diluído em muitos ciclos.
- Peças com design complexo ou que exigem alta precisão e detalhes finos.
- Aplicações em que o acabamento e a qualidade estética são críticos desde a saída do molde.
- Indústrias como automotiva, eletrônica, brinquedos, saúde, e qualquer área que requer peças técnicas de alta precisão.
Cada processo tem seu lugar dependendo das necessidades específicas do produto, quantidade a ser produzida e orçamento disponível.
Solicite um contato comercial
Solicite sua cotação com a Luan! Desenvolvemos, produzimos e comercializamos peças em Vacuum Forming, priorizando qualidade e satisfação. Somos certificados pela NBR ISO 9001:2015.